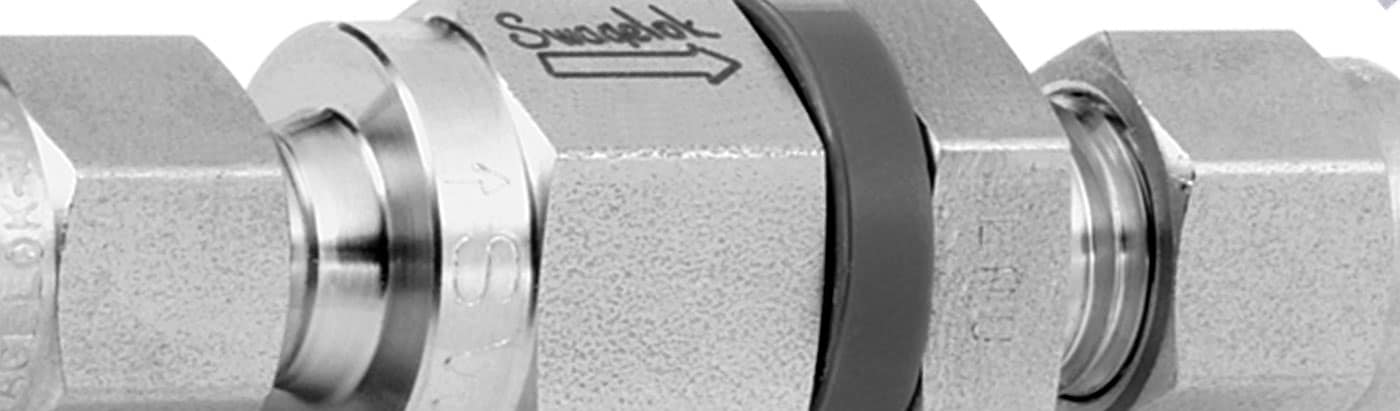
Swagelok® 체크 밸브 및 초과 누출 차단 밸브
Swagelok 인라인 체크 밸브는 일반 용도 및 고순도 애플리케이션에서 역류를 제어하는 제품이며 조절 가능하거나 고정된 크래킹 압력 범위로 공급됩니다. 초과 유량 차단 밸브는 바이패스 메커니즘의 필요성을 없앰으로써 시스템의 무결성과 안전성을 높여줍니다.
체크 밸브 | 한 방향으로 유체 유동을 제어하도록 설계됩니다
초과 유량 차단 밸브 | 다운스트림으로 초과 유량이 방출되는 것을 막습니다
Swagelok® 체크 밸브는 유체의 한 방향 유동만 허용하도록 설계되었습니다. Swagelok 체크 밸브는 일반 서비스에 사용되는 포펫, 리프트, 완전 용접형 버전 또는 중압 또는 고압을 포함한 고순도 애플리케이션 등의 다양한 구조로 공급 가능합니다.
Swagelok 체크 밸브는 다양한 연결구와 씰 재질로 공급 가능하므로, 사용자가 자사 시스템 및 공정 유체와 호환되는 통합하기 쉬운 솔루션을 찾을 수 있습니다. 특정 Swagelok 체크 밸브에는 고순도 애플리케이션에서 시스템 유체를 신뢰성 높게 밀폐할 수 있는 완전 용접형 구조가 적용되어 있으며, 일부는 압력 강하를 줄이고, 무유동 영역을 없애며, 탁월한 누설 무결성을 제공하는 동시에 유량을 극대화할 수 있도록 초고순도 플루오르수지(fluoropolymer)로 구성되고 O-링이 없습니다.
Swagelok® XS 시리즈 초과 유량 밸브에는 다운스트림에서 초과 유량이 발생하면 트립 위치로 이동하여 시스템 유체의 통제되지 않는 방출을 막는 슬롯형 포펫이 있습니다. 그다음, 압력이 균등화되면 재설정됩니다. 이 밸브는 복잡한 바이패스 메커니즘이 필요 없으므로 유지보수 시간이 절감됩니다.
체크 밸브가 올바르게 작동하는지 확인하려면 크래킹 압력과 리씰 압력 사이의 차이를 알아보십시오.
Check Valve Categories
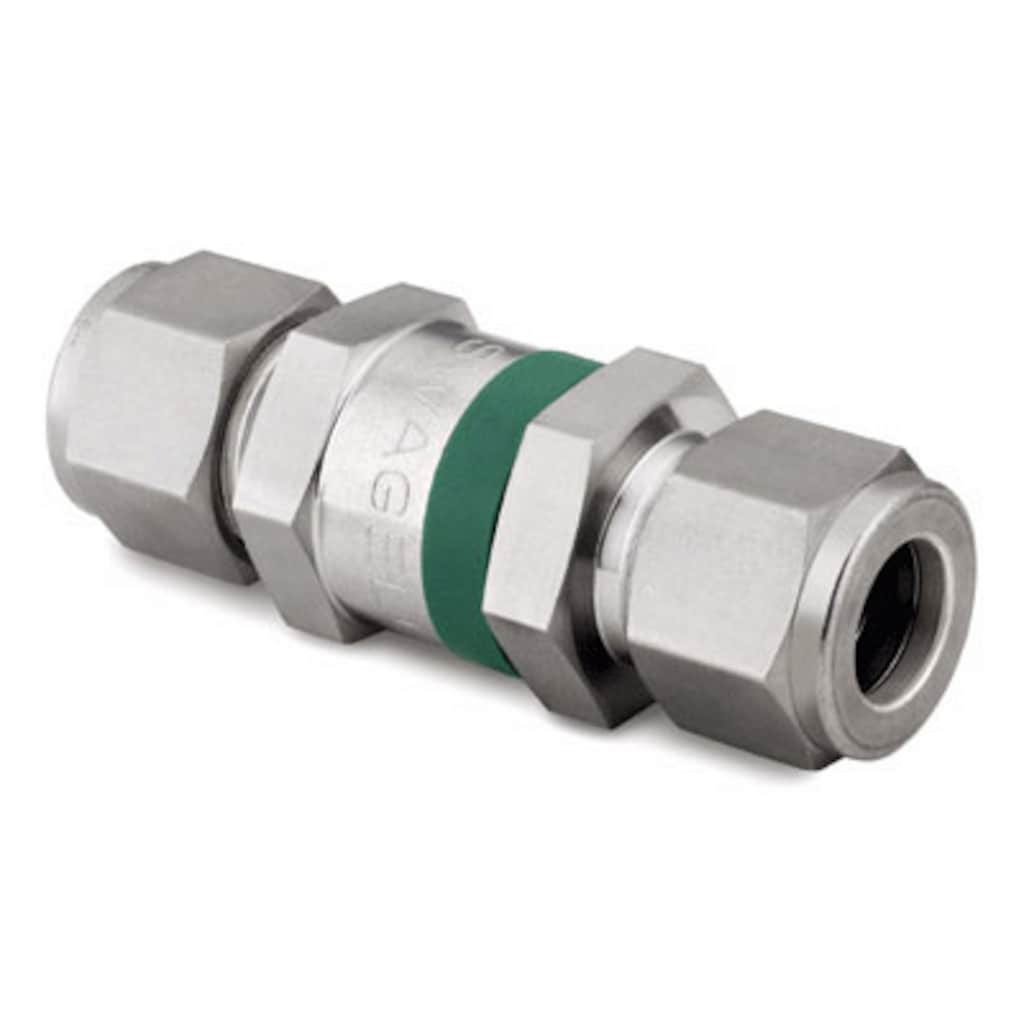
Excess Flow Valves
Enhance system safety by preventing uncontrolled release of system media if downstream line ruptures with excess flow valves.
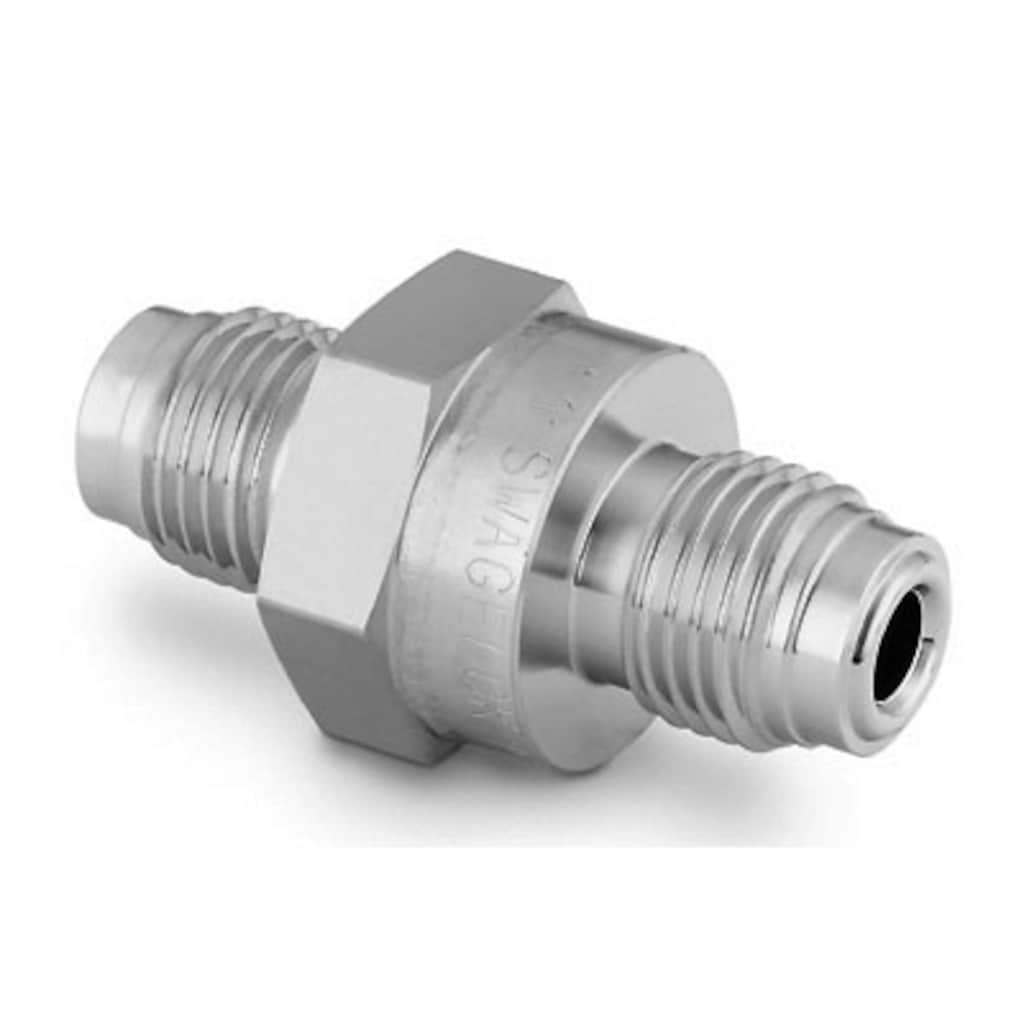
High-Purity Welded Check Valves, CW Series
The all-welded design of high-purity welded check valves provides reliable containment of system fluid while the 316L SS body offers enhanced material purity.
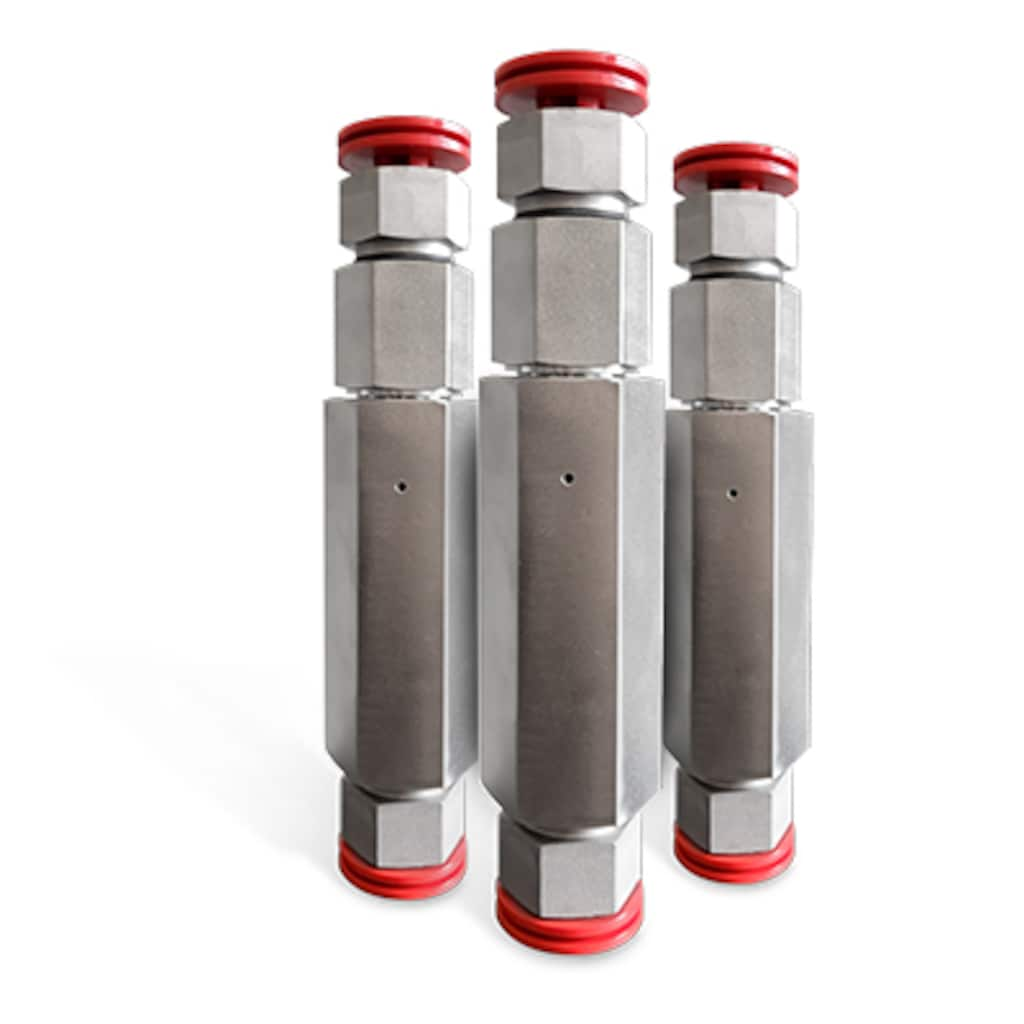
Hydrogen Check Valves
Enhance safety in hydrogen applications with Swagelok® hydrogen FK check valves, offering reliable shut-off, unidirectional flow, and high-pressure support.
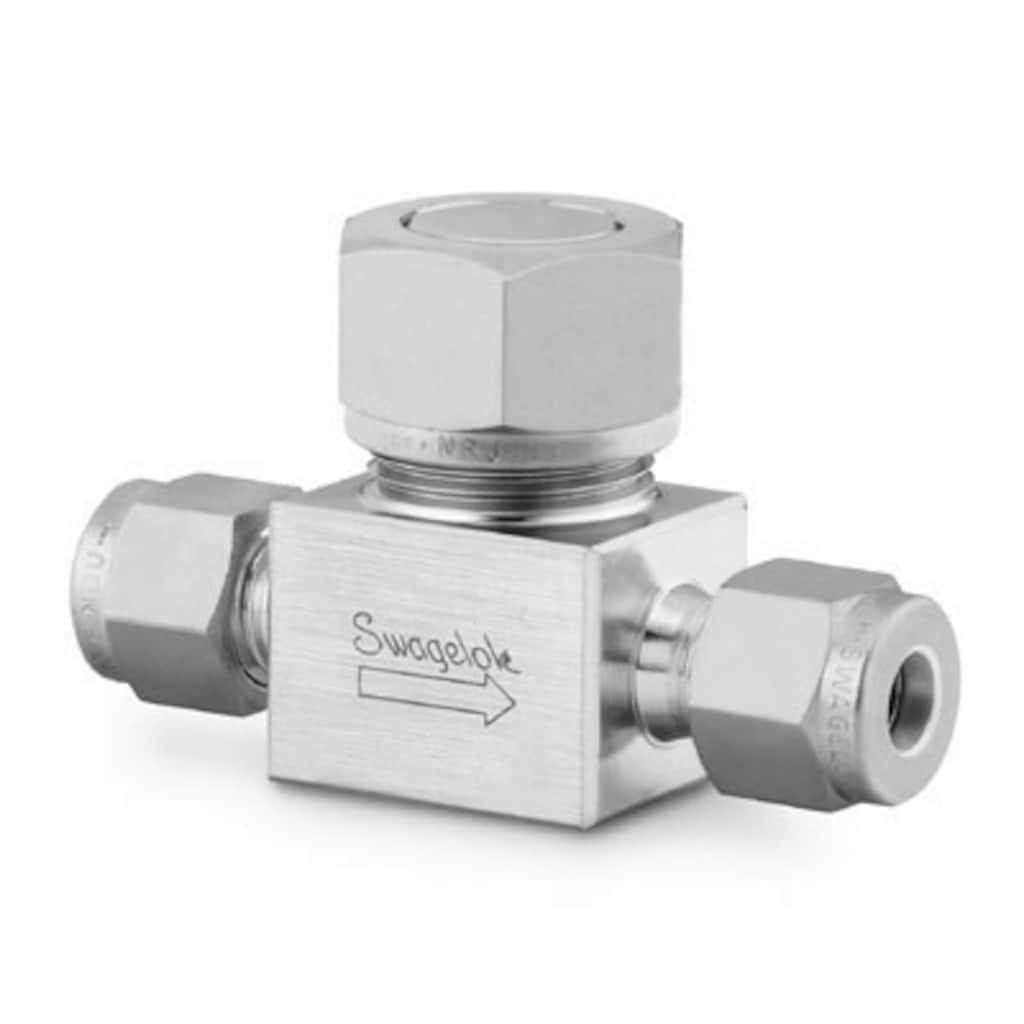
Lift Check Valves, 50 Series
Rugged, all-stainless steel lift check valves limit reverse flow under pressures up to 6000 psig (413 bar) and temperatures up to 900°F (482°C).
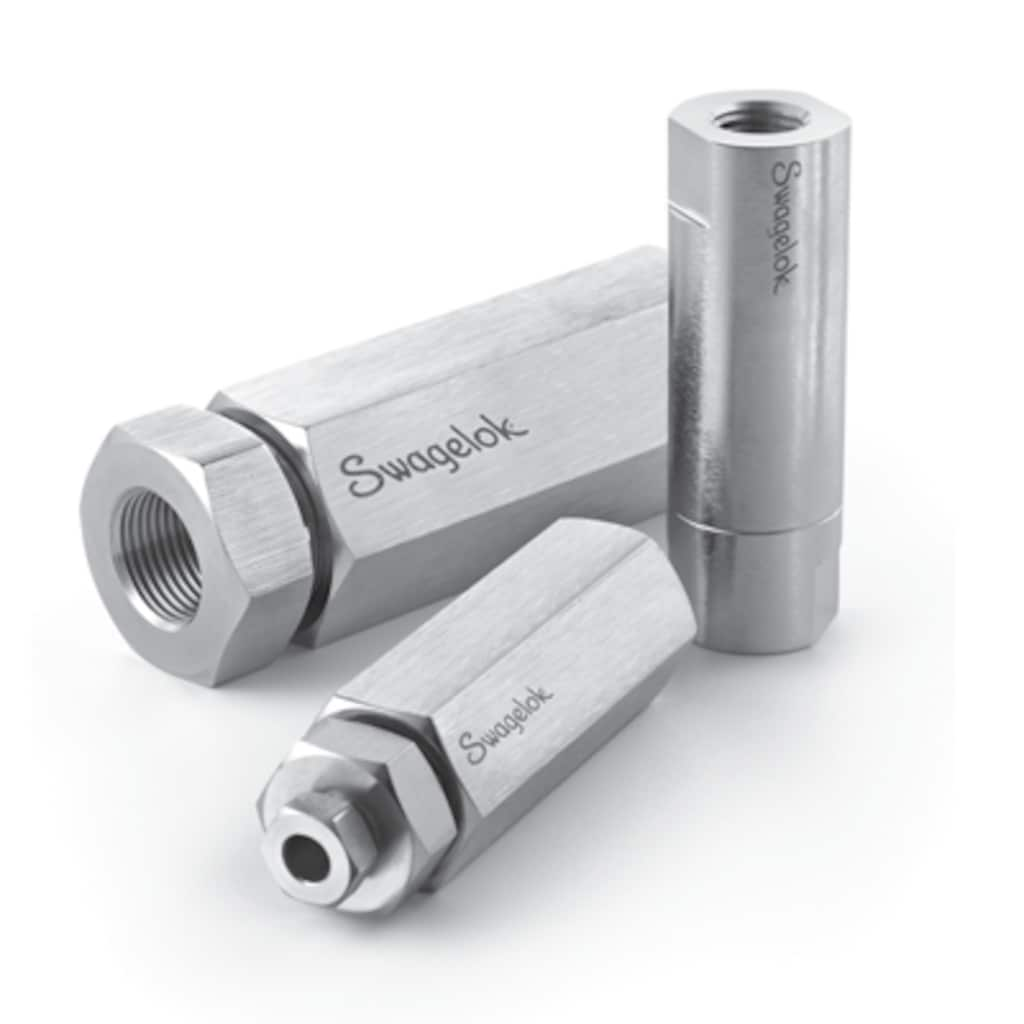
Medium-Pressure Check Valves, CV Series
The medium-pressure check valves are designed for system pressure containment and fluid control to prevent backflow.
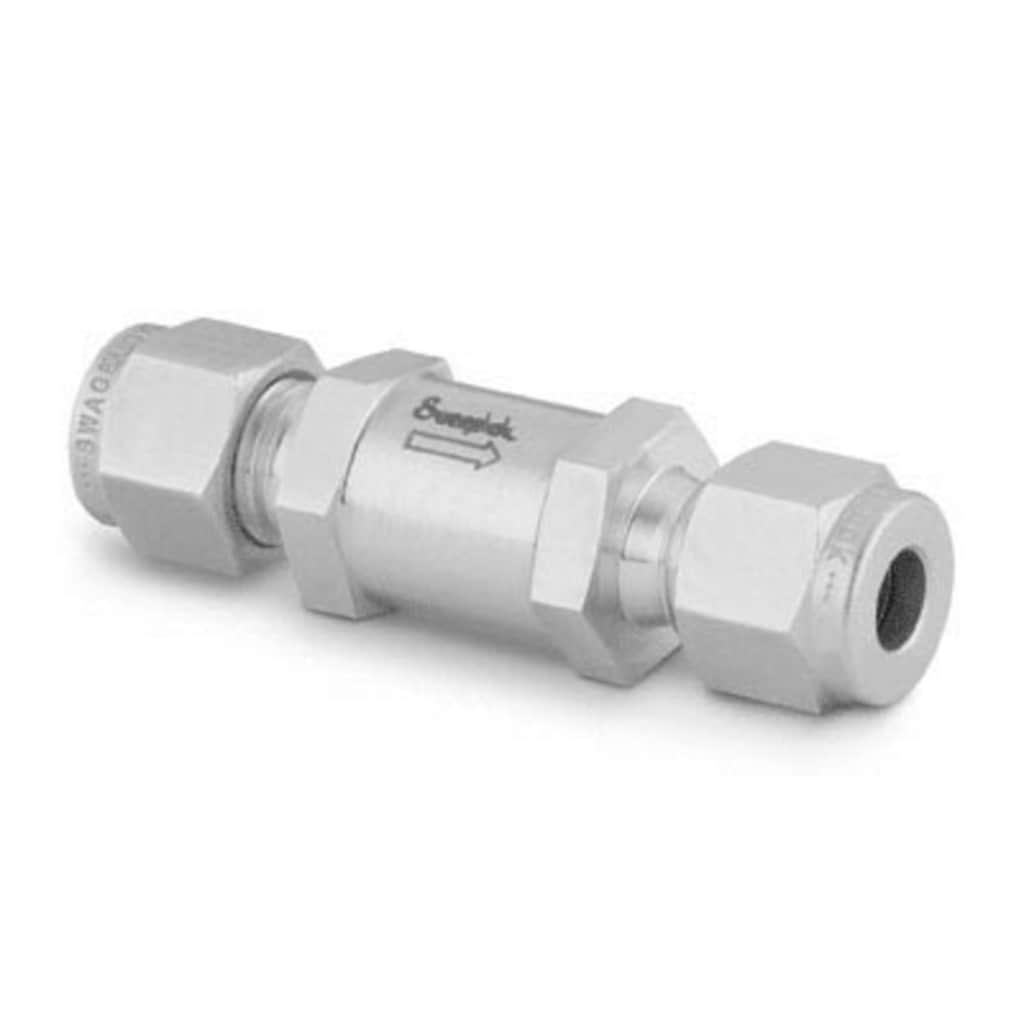
Poppet Check Valves, C, CP, CH Series
Browse stainless steel and brass poppet check valves, available with a variety of end connections and adjustable or fixed cracking pressures.
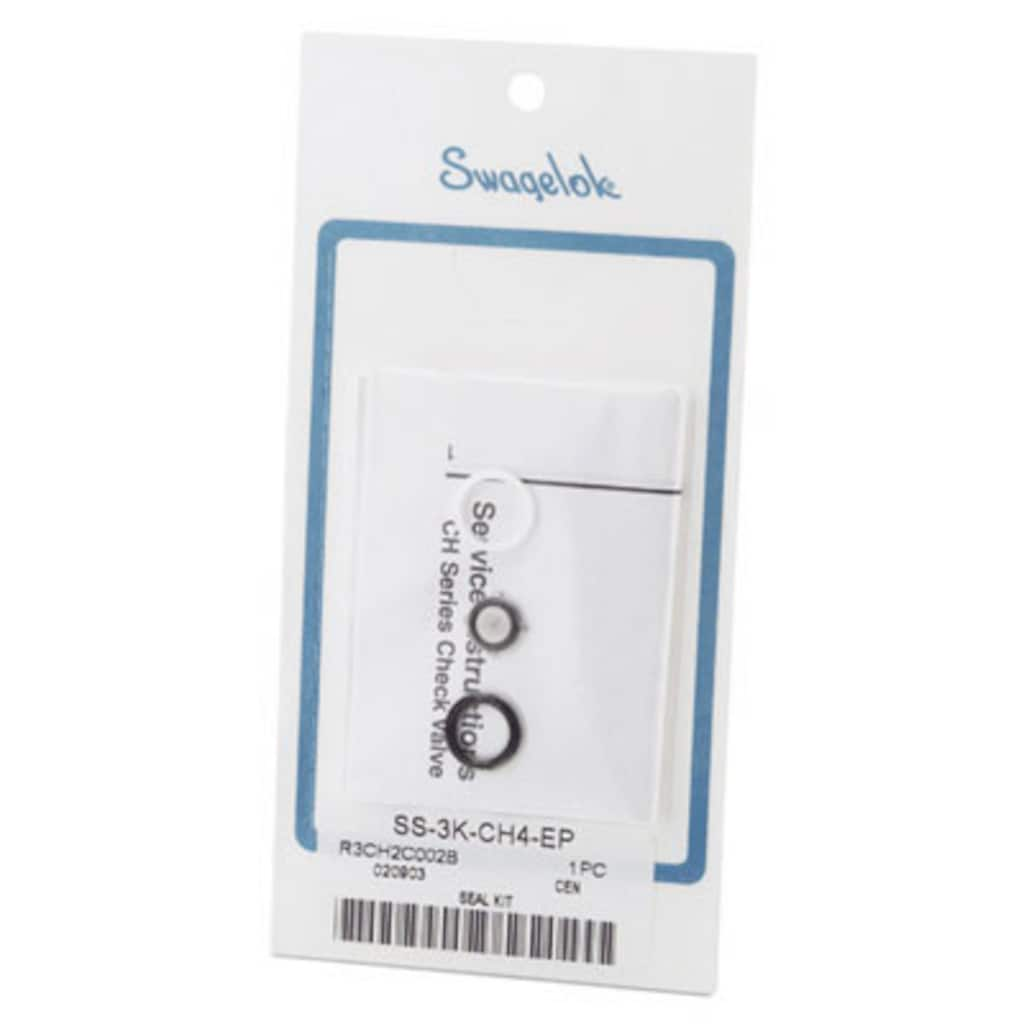
Spare Parts and Accessories
Browse deflector caps and a variety of poppet check valve maintenance accessories—including spring, seal and poppet replacement kits.

Ultrahigh-Purity Polymer Check Valves, CHP Series
Our ultrahigh-purity fluoropolymer check valves meet SEMI Standard F57-0301 and provide low cracking pressure while maximizing flow and reducing pressure drop.
체크 밸브 카탈로그
구성 재질, 압력 및 온도 등급, 옵션, 액세서리를 포함한 자세한 제품 정보를 찾을 수 있습니다.
Features: Working pressures up to 6000 psig (413 bar); Adjustable and fixed cracking pressures Variety of end connections; 316 stainless steel and brass materials
Swagelok® offers medium- and high-pressure fittings, tubing, valves, and related accessories with temperatures up 1000°F (537°C), pressure ratings up to 60 000 psig (4134 bar) in sizes ranging from 1/4 to to 1 in. for medium-pressure products and 1/4 to 9/16 in. for high-pressure products. NACE® MR0175/ISO15156 compliance is available.
Features: All-welded design provides reliable containment of system fluid; Forward flow starts at less than 2 psig (0.14 bar) pressure differential; Valve closes with less than 2 psig (0.14 bar) back pressure; 316L SS body offers enhanced material purity
Features: Alloy 625, alloy 825, and Alloy 2507 super duplex stainless steel materials; Available for CH4 adn Ch8 series check valves; Working pressures up to 6 000 psig (413 bar); 1/4 to 1/2 in. Swagelok tube fitting or NPT end connections; Fixed cracking pressures: 1 to 25 psi (0.07 to 1.8 bar)
Features: Modified PTFE wetted components meet SEMI Standard F57-0301 for ultrahigh-purity system components; Fine thread flare and Nippon Pillar® Super 300 end connections; Low cracking and reseal pressure
Rugged, all-stainless steel construction; Reverse flow coefficient less than 0.1 % of forward flow coefficient; No springs or elastomers; Compact size
Stop uncontrolled release of system media if downstream line ruptures. Features: Pressures up to 6000 psig (413 bar); Temperatures up to 400°F (204°C); 1/8 to 1/2 in. and 6 to 12 mm end connections; Stainless steel construction
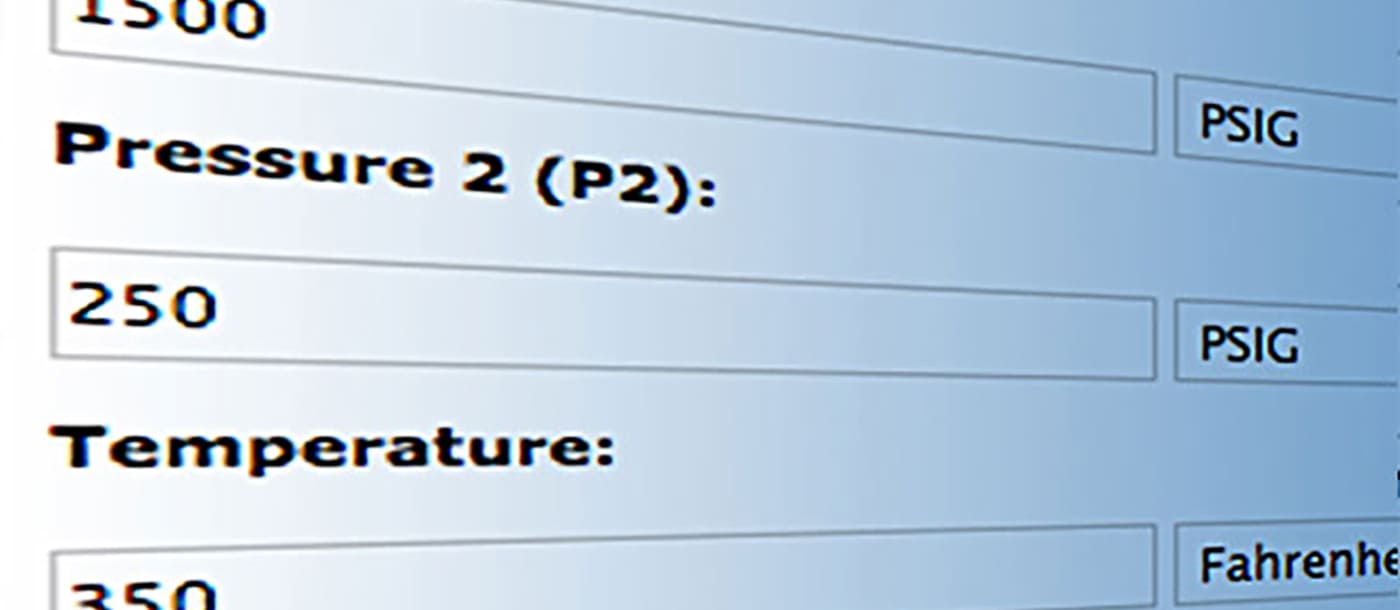
Swagelok Resources Curated for You
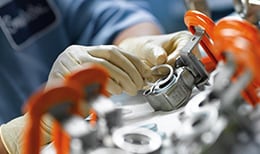
산업용 유체 시스템에 적합한 밸브를 선정하는 방법
산업용 유체 혹은 샘플링 시스템 설계 애플리케이션에 가장 적합한 밸브를 선정할 때 유용한 STAMPED 방법을 어떻게 적용하는지 소개합니다.
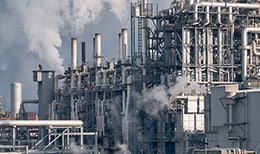
누출 저감(Low-E) 밸브로 비산 누출 비용 최소화
비산 누출은 화학 및 정유 산업에서 점점 더 큰 문제로 대두되고 있습니다. 인증 받은 누출 저감(Low-E) 밸브를 사용하면 시설과 수익성을 보호할 수 있습니다. 이 게시글에서 누출 저감 밸브가 무엇인지, 어떤 테스트를 거치는지, 플랜트에 어떻게 도움이 되는지 알아보십시오.
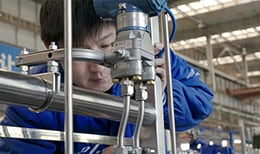
선양 고풍기 유한공사(Shenyang Blower Works Group)의 안전 및 신뢰성 개선 사례
선양 고풍기 유한공사(Shenyang Blower Works Group)가 안전과 생산 효율성을 개선하는 동시에, 일관성, 신뢰성, 고객 비용 절감을 실현할 수 있도록 Swagelok Shanghai가 어떻게 지원했는지 알아보십시오.
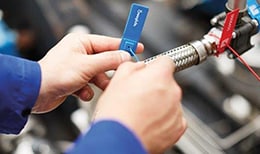
밸브 및 호스 태그로 유지보수 프로그램을 개선하는 방법
Swagelok 전문가 두 명이 산업용 유체 시스템 전반에 걸쳐 호스와 밸브에 견고한 태깅 시스템을 적용하여 유지보수를 간소화하고 시스템 가동 중단을 최소화할 수 있는 방법을 어떻게 설명하는지 읽어보십시오.