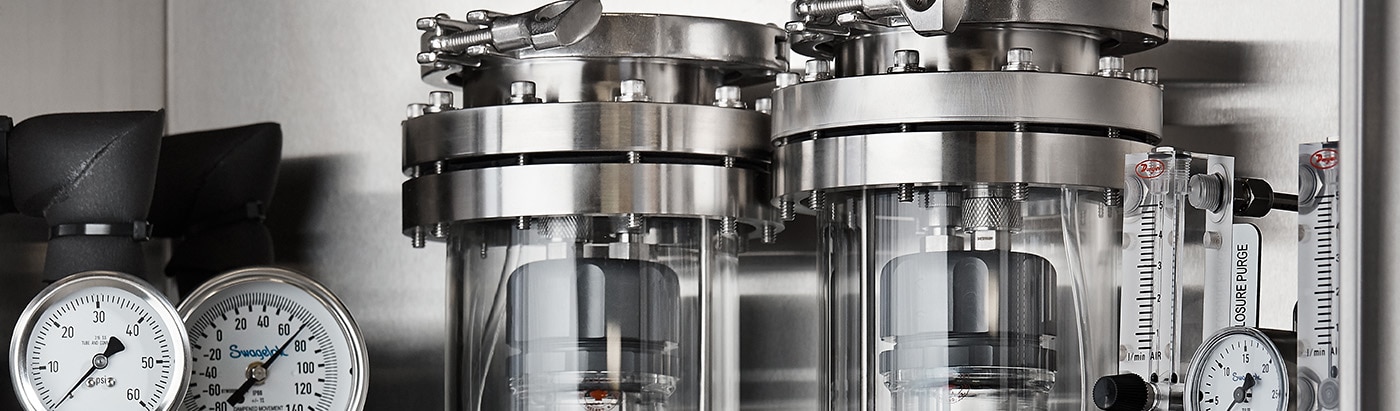
Ammoniak-Probenahmesystem von Swagelok®
Das Ammoniak-Probenahmesystem von Swagelok ermöglicht eine sicherere Probennahme von wasserfreiem Ammoniak, da die Exposition der Mitarbeiter gegenüber flüssigem und gasförmigem Ammoniak verringert wird. So werden einheitliche und deutlich schnellere Probenahmeprozesse gewährleistet und der Transport der Ammoniakproben durch die Anlage entfällt.
Einen Experten für Probenahme kontaktierenAmmoniak kommt in der Herstellung von Düngemitteln, Kunststoffen, Textilien, Erdöl und vielem mehr zum Einsatz. Um ammoniakinduzierte Spannungsrisskorrosion in Lagertanks und damit verbundene Probleme bei der Produktqualität zu vermeiden, muss anhand einer regelmäßigen Probenahme sichergestellt werden, dass der Wassergehalt im Produkt zwischen 0,2 % und 0,5 % liegt.
Das geschlossene Probenahmesystem für Ammoniak wurde speziell von Swagelok entwickelt, um die gängigen Probleme bei der Entnahme von Ammoniakproben zu vermeiden. Das Ammoniak-Probenahmesystem von Swagelok zeichnet sich durch verschiedene Merkmale aus:
- Abgeschlossene Probenhalterungen: Ausgestattet mit abgeschlossenen Probenhalterungen, bietet das System eine höhere Sicherheit, da die Expositionsrisiken der Mitarbeiter sowie emissionsbedingte Umweltschädigungen minimiert werden. Durch die geschlossene Probenahme werden die PSA-Anforderungen für Bediener reduziert. Das gläserne Design ermöglicht eine visuelle Prüfung des Probenzustands. Es ist mit einfacher oder doppelter Halterung erhältlich.
- Vorgekühlte Probenröhrchen: Mithilfe von kaltem Ammoniak wird in einem Kältebad die Wärme aus der Halterung und dem Probenröhrchen abgeleitet, sodass eine exzessive Verdampfung und damit Probleme im Hinblick auf die Probengenauigkeit vermieden werden. Der Füllstand des Kältebads wird über ein höher gelegenes Ablaufröhrchen kontrolliert. Bei der Befüllung des Kältebads wird altes Ammoniak aus der Leitung entfernt, sodass eine frische Probe entnommen werden kann. Über das Ammoniak-Fast-Loop-Modul werden die Probenahmeventile gekühlt, während die Probenahmeleitungen über konzentrische Schläuche vorgekühlt werden.
- Halbautomatisierte Dosierung: Für eine verbesserte Abfüllung ist das Probenröhrchen mit einer Verschlusskappe ausgestattet. Bei Befüllung des Probenröhrchens wird mithilfe der Verschlusskappe sichergestellt, dass eine präzise Probenmenge entnommen wird. Die Verschlusskappe wird oben auf das Röhrchen aufgesetzt und dient zur Kontrolle des Füllstands. Überschüssige Mengen fließen in das Kältebad ab, sodass eine einheitliche Probengröße gewährleistet ist. Die Probenröhrchen sind in Größen von 100 ml oder 250 ml erhältlich.
- Bedienung mit einem Handgriff: Für eine einfache Bedienung und zur Vermeidung von Bedienfehlern wird die Probenahme mit einem einzelnen Handgriff gesteuert. Über einen Zahnradmechanismus werden mit einem einzigen Handrad vier Ventile auf die folgenden Positionen eingestellt: „Aus“, „Spülung“, „Kühlung“ und „Probenahme“. Für eine noch bessere Kontrolle bei der Inbetriebnahme und Instandhaltung können optional zusätzliche Kontrollventile vorgesehen werden.
- Heizgerätesteuerung per Touchscreen: Das Heizgerät kann bequem per Touchscreen bedient werden, um einheitliche Ergebnisse zu erzielen und eine übermäßige Erwärmung zu vermeiden. Die benutzerfreundliche und intuitive Oberfläche mit Schritt-für-Schritt-Anleitungen sorgt dafür, dass Bedienerfehler auf ein Minimum reduziert werden.
Unsere erfahrenen Fluidsystemingenieure stimmen alle Analysegeräte optimal auf Ihre Spezifikationen ab. Alle Ammoniak-Probenahmesysteme von Swagelok werden gründlich geprüft und sind durch die eingeschränkte Nutzungsdauergarantie von Swagelok abgedeckt.
Erfahren Sie mehr über Sicherheit und Effizienz bei der Probenahme von Ammoniak
Überblick zu unseren Anwendungsleitfäden
Detaillierte Informationen zu unseren Baugruppen anfordern
This manual contains installation, operation, and maintenance information for the safe and effective operation of the Swagelok® Ammonia Sampler.
The Swagelok® ammonia sampler is a closed-loop sampling unit that minimizes exposure to the operator and introduces consistency into the sampling operation.
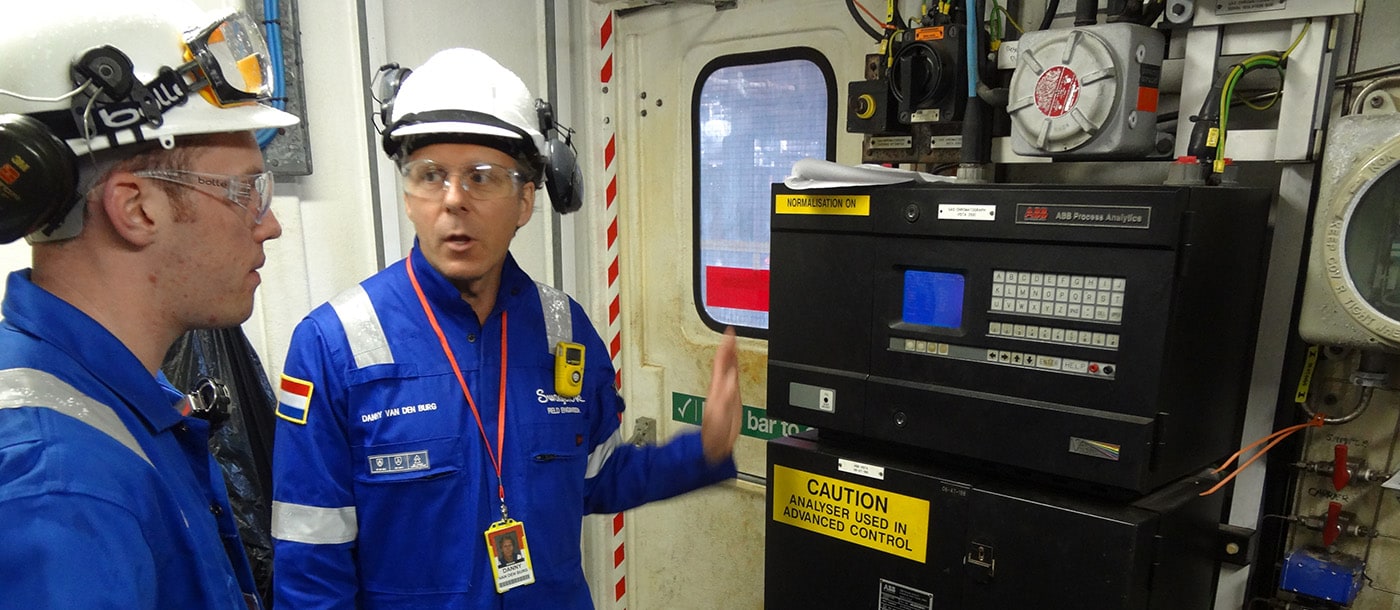
Evaluierungs- und Beratungsservices von Swagelok
Ob bei der Probenahme von Ammoniak oder anderen Fluiden und bei sämtlichen Herausforderungen in Ihren Fluidsystemen können Ihnen die Swagelok-Experten im Rahmen eines Vor-Ort-Besuchs aufzeigen, wie Sie Ihre betriebliche Produktivität steigern, potenzielle Sicherheits- und Umweltprobleme minimieren und eine optimale Systemleistung und -effizienz gewährleisten.
Umfassender Support bei der ProbenahmeRessourcenzentrum
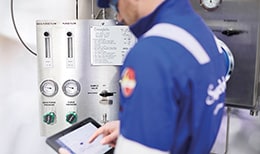
Wie Sie Emissionen an Probenahmestellen reduzieren
Raffinerien sowie chemische und andere Anlagen sind stets auf der Suche nach Möglichkeiten zur Minimierung flüchtiger Emissionen. Ein geschlossenes Probenahmesystem kann hier eine relativ einfache und kostengünstige Lösung darstellen.
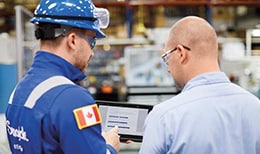
Genauigkeit bei der Probenahme—Die besten Tipps für erfolgreiche Ergebnisse
Mit unseren Tipps stellen Sie sicher, dass Ihr industrielles Probenahmesystem künftig genauere und repräsentativere Proben liefert.
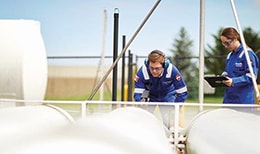
Field Engineers im Interview: Wie unser Global Engineering Team Ihnen dabei helfen kann, die Leistung Ihrer Fluid- und Probenahmesysteme zu verbessern
Unsere Field Engineers unterstützen Betreiber von Fluid- und Probenahmesystemen bei der Lösung ihrer Probleme—von Leckagen bis hin zu Ungenauigkeiten bei der Probenahme. In diesem Artikel erfahren Sie alles, was Sie über die Services der Field Engineers bei Swagelok wissen sollten.
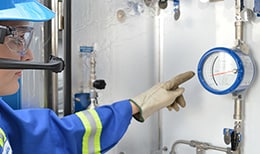
Checkliste zur Sicherheit in industriellen Fluidsystemen
Mit diesen Best Practices steigern Sie die Sicherheit Ihrer industriellen Fluidsysteme.